Construction, eNews
The ripple effect: Unpredictable material shortages disrupt construction industry
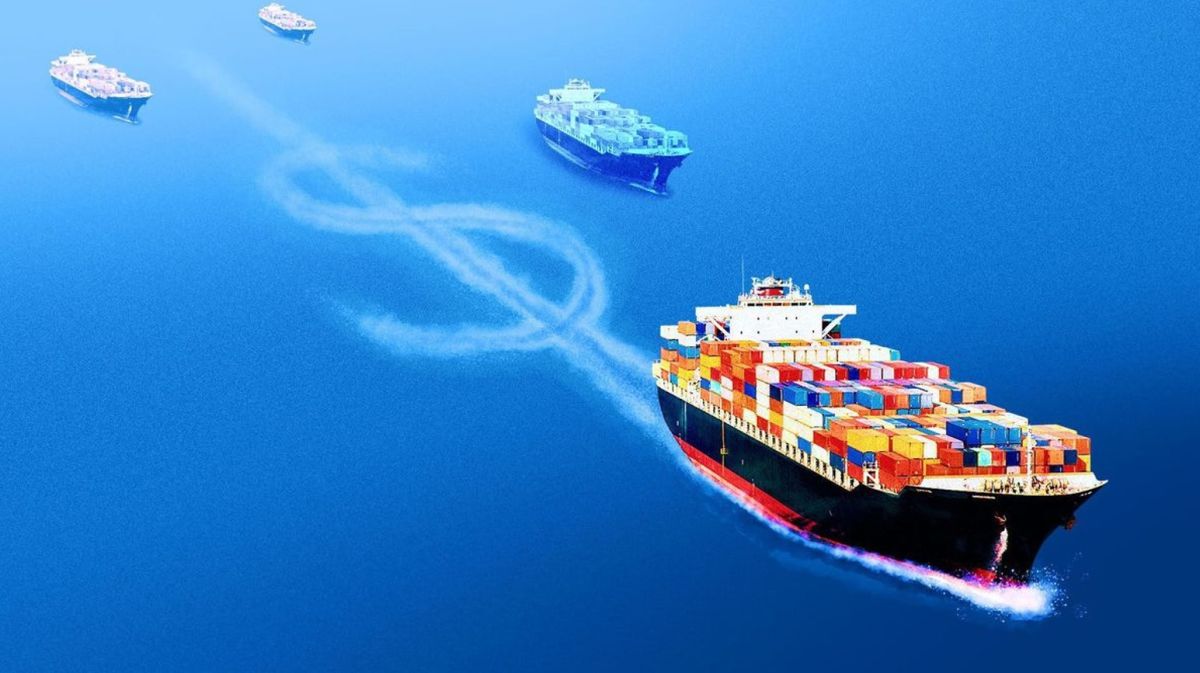
The supply chain, consisting of individuals and companies involved in the production and delivery of products to customers, can be very delicate. A single disruption has the ability to trigger a ripple effect, significantly impacting various industries worldwide. Material shortages, such as those affecting lumber, metals and food, are among the factors influencing the supply chain.
Why it matters: Material shortages can cause disturbances that impact credit professionals’ ability to service customers. In the construction industry, these shortages can delay projects and result in withheld customer payments.
By the numbers: According to a recent eNews poll, 32% of credit professionals surveyed reported that material shortages are a leading cause of challenges in meeting customer needs.
A combination of geopolitical issues and supply-demand imbalances have prompted a critical material shortage. This is particularly evident in the base metals market, where analysts are forecasting a notable shortfall in light metal supply in 2025, according to a recent Reuters report. “Median forecasts for copper, tin, nickel and lead have all been cut since Reuters’ last quarterly poll in October, reflecting concern about the demand impact from a tariff trade war,” the article reads.
As housing demands and labor shortages persist, the availability of lumber has decreased. Most recently, tariffs on Canadian lumber have further exacerbated these shortages. In fact, several large sawmills in Canada have announced production cuts, reducing overall lumber supply in North America. As a response to Trump’s proposed 25% tariff policy, targeting key goods such as energy (oil, natural gas and electricity), timber and lumber products exported from Canada to the U.S., Canada enacted tariffs on $30 billion in goods imported from the U.S., effective March 4, 2025, according to the Government of Canada.
How it’s impacting construction credit
Construction companies often establish long-term relationships with suppliers to maintain a steady flow of materials. When tariffs are suddenly introduced or increased, these supply chains can be interrupted, leading to delays and shortages.
Scarcity in metal and lumber can delay construction projects, as material suppliers struggle to deliver materials on time. “If you promised a shipment in May but later find out it won’t ship until September because of the shortage, and your customer needs to complete the job before that, it can severely impact their ability to proceed on that project,” an NACM member said.
As a result of material delays, customers can withhold payment, leaving suppliers with outstanding accounts receivable for shipped but uninstalled goods. “You might even face back charges for not providing materials promptly,” said an NACM member. “This, in turn, can affect whether you receive full payment for the job.”
Severe weather events contribute to material shortages; wildfires in Southern California significantly affect lumber costs and the construction industry as a whole. “The urgent need for rebuilding efforts in the wake of the fires will dramatically increase the demand for lumber, plywood, sheeting, decking and framing materials,” reads a Construction Management article. “This sudden surge in demand will inevitably drive prices up as suppliers struggle to keep pace with the increased orders.”
When a natural disaster, like a tornado, shuts down ports and disrupts manufacturing, it can create challenges for material suppliers. According to an eNews poll, 31% of credit professionals reported that natural disasters have impacted their ability to service their customers. “We’ve experienced significant damage to a couple of branches during previous hurricanes,” said Tom Long, CCE, credit and collections manager at Empire Pipe & Supply Co., Inc. (Birmingham, AL). “One way we address this is by shipping materials from other branches to our customers. However, when a branch is impacted, it typically means widespread damage in the area, affecting most of our customers—many of whom may also be shut down.”
The bottom line: Material shortages are a significant challenge, impacting supply chains, project timelines and financial transactions. Credit professionals must stay vigilant and adaptable, finding ways to mitigate these disruptions and maintain business continuity.